Home>Bearing knowledge>The reason and avoidance of grinding cracks in carburized and quenched parts |
/*728*90 created on 2018/5/16*/ var cpro_id = "u3440131";
Causes and avoidance of grinding cracks in carburized and quenched parts
Source: China Bearing Network Time: 2017-10-16
/*250*250 was created on 2017/12/25*/ var cpro_id = 'u3171089'; |
It is well known that the cracks formed under the effect of the tensile stress generated by the grinding process are called grinding cracks. If the surface treatment is performed without such stress (for example, pickling, plating, oxidation, etc.), it is not found. Hydrogen embrittlement and stress corrosion cracking; and the crack formed by the above surface treatment under the effect of grinding stress; I believe that it can also be in the field of grinding cracks.
The causes of the grinding cracks are different; and sometimes they are comprehensive effects; their shapes can usually be divided into three types: 1) the direction of the grinding crack is common to the direction of rotation of the grinding wheel; and it is slightly connected; 2) the direction of the crack and the grinding wheel The direction is common; the adult fish is phosphorus-like and slightly discontinuous; 3) the crack is formed during the external treatment due to the grinding stress. The crack is intermittently a sharp-pointed longitudinal feather-like crack [1]. Avoid constituting these The method of cracking is to reduce the grinding stress from all aspects.
1 Falling carburized layer itself uneven stress carburizing layer Carbohydrate particles are finer as much as possible; the more uniform the carbide dispersion, the better. In order to avoid carbide coarsening; obtain extremely dispersed carbides [2]; controllable gas Selection of source; is a very important factor [3]. For example: the primary component of natural gas is CH4. For the current carburizing gas source; usually the carburizing mechanism is CO→Cad+CO2 (Cad is activated carbon). Only natural gas can be directly cracked to produce activated carbon carburizing [4] CH4 → Cad + 2H2; and when natural gas purification is very good (organic sulfur ≤ 3 ~ 5mg / m3, inorganic sulfur ≤ 1 ~ 3mg / m3, carbon dioxide ≤ 0. 5mg/m3)[5] This cracking reaction is more complete; the gas consumption of natural gas after purification is greatly reduced. For example: Changchun FAW Volkswagen three 1000 kg Ai Xie Lin multi-purpose furnace and a 12-plate Ai Xielin through-type multi-purpose furnace The output value of four 1000 kg Ai Xie Lin multi-purpose furnace. The original gas source is about 40M3/h; after the natural gas purification equipment is used; only 23M3/h; the thickness and dispersion density of the carbon black and non-martensitic arrangement of the parts are greatly increased. Improvement; usually <3μm (shallow corrosion) [5]; carburized layer carbide grain size is also improved. Sichuan heavy-duty car Also reached a similar effect; only the material gas saving more than 40 million / year.
2 In order to make the transformation of martensite the most stressful. North 湫 I 沧钚. 淙 橹 橹 橹 橹 ≡裰 ≡裰 ≡裰 ≡裰 ≡裰 ≡裰 ≡裰 ≡裰
During quenching and cooling; the two stresses of thermal stress (heat rise and contraction stress) and arrangement stress cancel each other; the more offset, the better. The non-martensitic arrangement of the carburized quenching part should be reduced; the gas source selection is the primary factor [3] 5); quenching oil is second. Quenching oil demand passes through the pearlite transformation zone; while in the martensite transformation, it is necessary to reduce the stress to avoid deformation and to moderately cool, especially for carburized parts with large cross section; Care should be taken to avoid unqualified core hardness; the amount of retained austenite is added; therefore, the cooling in the martensite transformation zone is determined according to the steel number and the cross-section size of the part. The cooling rate in the quenching oil depends mainly on the type of cooling oil. Factors, ingredients, additives, etc. Proper improvement of the oil temperature of the quenching oil can be very effective; but when the oil temperature is raised to 120-140 ° C; many isothermal oils are too slow at 300 ° C; therefore, the cross section is large The amount of retained austenite in the part is added; the hardness of the core is reduced. After the proper improvement of the cooling rate of the isothermal oil at 300 ° C to deal with this problem. The quenching oil of the Changchun FAW-Volkswagen Ai Xie Lin multi-purpose furnace is the product of Germany's Bedofia; Use 60~80 ; Flash point of 187 deg.] C; fast cooling temperature; subcooled not slow large deformation part; general car parts deformed about 15 filaments.
It is necessary to reduce the deformation; the high temperature cooling of the oil should be moderate and the low temperature cooling should also determine the appropriate cooling rate according to the steel grade and the cross-section of the part; properly raise the oil temperature to 120-140 °C to reduce the deformation; and avoid the addition of retained austenite. And the hardness of the heart is reduced.
3 The retained austenite of the carburized layer is under the effect of grinding stress; induced martensitic transformation.
This stress-induced martensite is untempered martensite; the stress is large; the metallographic investigation has obvious bright regions around the crack; this bright region is usually the stress-induced martensitic transformation region.
The amount of retained austenite; directly related to the steel grade, the size of the carburized part, the quenching oil cooling rate, the oil temperature, etc. because of various reasons; many companies with better equipment; the preferred oil is Derunbao, Isothermal oil from companies such as Houghton and Uncon; the quality of heat treatment is reliable, long life and stable; but expensive.
At present; Haisen HSGKD-2 type fast light is specially equipped with isothermal oil; it has been tested by Ai Xielin multi-purpose furnace of Chongqing Cangzhou Gear Factory for 4 years; now the two Ai Xie Lin multi-purpose furnaces have been converted to Heisen products; In addition; Rehabilitation Electromechanical Equipment Factory Ai Xie Lin multi-purpose furnace; Hunjiang Gear Factory Hucklov and imitation Ai Xilin multi-purpose furnace; Chongqing Nonferrous Metal Research Institute; Fengdong furnace, etc. all use Heisen HSGKD-2 type products. The products are classified into four categories: A, B, C and D; they are supplied to the special needs of each plant. The quenching hardness, metallographic arrangement and deformation of the heat-treated products are satisfactory; the cost of the imported oil is greatly reduced.
4 Influence of chemical composition of carburized and quenched steel
4.1 Usually for boron-added carburized steel; pay attention to the composition of the grain boundary boride. The composition of the boride makes the grain boundary partial resistance (borax brittle); directly affects the composition of the grinding stress and the grinding crack source. In order to eliminate the composition of grain boundary boride in boron-containing steel; the first is to control the metallurgical quality from the thermal treatment point of view; the higher the austenitizing temperature and the slower the cooling rate; the more borides are enriched in the grain boundary When the cooling rate is faster; there is the ability to avoid the segregation of boride.
4. 2 pairs of carburized steel with titanium; pay attention to the formation of cubic titanium to reduce the tolerance of the grain boundary; directly affect the composition of the grinding stress and the source of the grinding crack. Eliminate the composition of the cubic titanium; Quality. From the point of view of thermal treatment; progressive austenitizing temperature; solid solution of cubic titanium in austenite; then cooling at an appropriate rate during cooling; avoiding enrichment of titanium at grain boundaries; The composition of crystalline titanium.
4.3 The handling of tin content is to avoid the formation of grain boundary tin compounds; the tin content needs to be controlled below 0.5%; together avoid tempering around 400 °C; usually carburized steel is tempered at low temperature; Arrangement is not easy to construct.
5 Grinding of grinding parameters
1) The grinding wheel grinding wheel size is preferably 100#. The coarser the particle size, the greater the stress.
2) The smaller the radial sway of the grinding machine and the grinding wheel, the better. The greater the sway; the greater the stress.
3) Wet grinding ratio dry grinding stress. ãƒ’é˜‚æŽ mold 舜胧徊 6. ㄆ诟.
4) The rotation speed of the grinding wheel is appropriate.
5) Control of the grinding wheel feed amount: the rough grinding amount should not be too large; the rough grinding can be controlled within 1~3 wire according to the hardness and steel number.
If necessary, add stress relief and tempering immediately after grinding; to reduce stress; together, stress-induced martensite arrangement is transformed into tempered martensite in time; to reduce internal stress. De-stress tempering temperature does not affect product function. In the case of demand for hardness, etc., it can be properly improved; to achieve the effect of reducing stress.
The reason for the feather-like crack formed by the surface treatment due to the effect of the grinding stress is that the center line of the grinding wheel inevitably changes in a cycle within a public service range; and the working surface also changes with the cycle of the center line of the grinding wheel; This periodic change causes the stress generated by the grinding to change as well; there is periodicity; the left-pointed right-thickness of the longitudinal feather-like crack indicates that the movement of the operation is from left to right. To avoid the crack; It is also possible to adopt appropriate methods to avoid hydrogen embrittlement and stress corrosion cracking during external surface treatment.
The leading process is adopted to make the non-martensitic arrangement of the carburized and quenched parts < 3 mm (shallow corrosion), so that the deformation of the parts is minimized (the pre-heat treatment process before machining is also useful); no further grinding is required.
Recommend to friends comments close window
Bearing related knowledge |
The basic layout analysis of the rolling bearing bearing professor describes the reason why the SKF bearing rust analysis: oil-free smooth bearing application features NSK bearing overheating reason and smooth, protective approach NSK high-precision angular touch ball bearing specification series layout composition
|
This article links to http://
Please indicate the bearing network http://
Previous:The development characteristics of high-viscosity gear pump: The rolling mill bearing must be steadily repaired and judged
China EPDM Deodorant,high quality Odors Absorbing Agent, with 75% Rubber Deodorant powder and 25% epdm material , the appearance is masterbatch , can be added in epdm masterbatch directly and well dispersed.
In rubber products, the rubber deodorant effectively lightens or removes odor or peculiar smell caused by rubber agent and rubber residual. It is especially applied to rubber products which are made of regrind materials.
It is of best thermal endurance, small dosage with long-time effect. And it has no effect on the property of rubber products requiring removing odor.
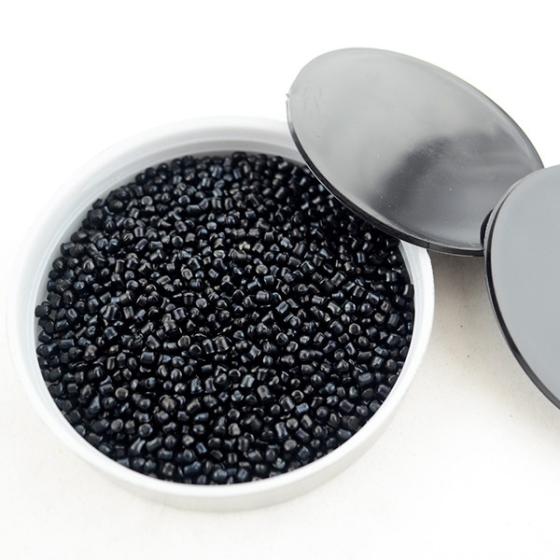
Epdm Deodorant
Epdm Deodorant,Agent Nature Deodorant,Odors Absorbing Agent,Polymer Odors Absorbing Agent
Ningbo Jiahe New Materials Technology Co.,ltd , https://www.cnjhchem.com